When discussing the differences between vector graphics and bitmap images, we touched upon a key characteristic of bitmap images—resolution. Indeed, resolution plays a crucial role in scientific image collection and paper preparation. This article will explore the definition of resolution, how to calculate it, and common issues related to it.
1. Definition of Image Resolution
Image resolution is a unique attribute of bitmap images, referring to the number of pixels contained within an inch of an image. It is measured in DPI (dots per inch), often referred to as "pixels per inch" or "dots per inch." Essentially, resolution determines the level of detail in an image, much like the concept of density in physics.
2. How to Calculate Image Resolution
When we know the physical size of an image and the number of its pixels, we can calculate the size of its resolution with the formula shown below.
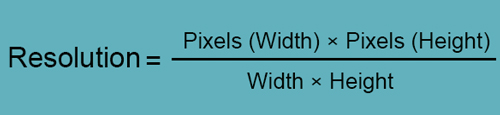
3. About image size
One thing to pay special attention to is that when we refer to image size, it is not the physical size of the image but the number of pixels (number size) in the drawing software. Usually, the larger the resolution, the finer the image. As shown in the following figure, the physical size of the same two diagrams, the more the number of its pixel grid, the finer the image.
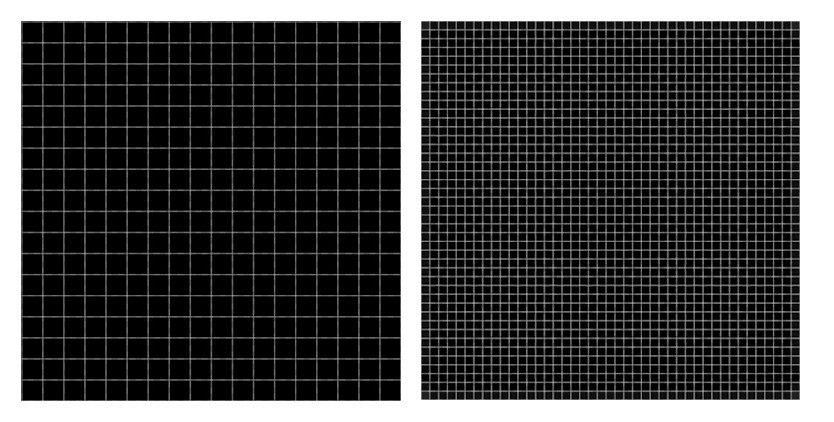
4. Frequently Asked Questions About Resolution
Q1: Since it is said that the larger the resolution, the finer the image, is it true that the larger the resolution, the better the image quality?
From this extreme example above, it seems that increasing the resolution does not affect the fineness of the image when the image has a single color. So, in the face of more complex color images, the resolution can be appropriately increased, while the color of a single image can meet the demand.
Q2:The difference between PPI and DPI.
ppi (pixels per inch): the sampling rate of the image (in the image, the number of pixels contained in each inch), refers to the smallest point of the screen can be resolved.
dpi (dots per inch): print resolution (the number of dots per inch that can be printed, that is, the printing accuracy), in general, can be understood as the smallest physical device can be resolved unit.
The two use different scenarios (screen and print), the definition is slightly different, can be generalized to some extent.
Q3:Can I put an image into Photoshop by directly increasing the resolution to make the image clearer?
It is possible to get Photoshop to increase the DPI, but there is no practical significance, because the total amount of information the image has has already been determined. If you increase the resolution at the same size, it will only result in an unrealistic enlargement of the pixels in the image (the extra pixels are calculated by difference); if you don't limit the size, you will change the size at the same time as you change the resolution. Therefore, the resolution should be determined at the beginning of the image drawing and not hope to change it later.
Q4:Are there any requirements for image resolution in journal submissions?
In journal submissions, generally for color portfolio images, the image requirements are 300 dpi or higher, depending on the journal's author submission guidelines.
For example, the author guidelines on the PNAS website have the following image resolution requirements:
Please supply high-resolution files whenever possible. Resolution of at least 1200 dpi is needed for all line art, 600 dpi for images that combine line art with photographs/halftones, and 600 dpi for images that combine line art with photographs/halftones. Resolution of at least 1200 dpi is needed for all line art, 600 dpi for images that combine line art with photographs/halftones, and 300 dpi for color or grayscale photographic images. Please review the PNAS Digital Art Guidelines.
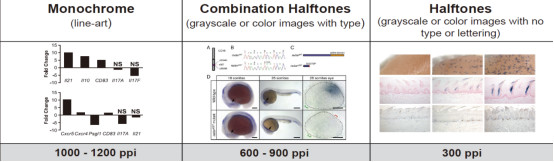